How Much Does a Mezzanine Floor Cost?
There are key elements to consider that influence the cost of installing a new mezzanine in your warehouse.
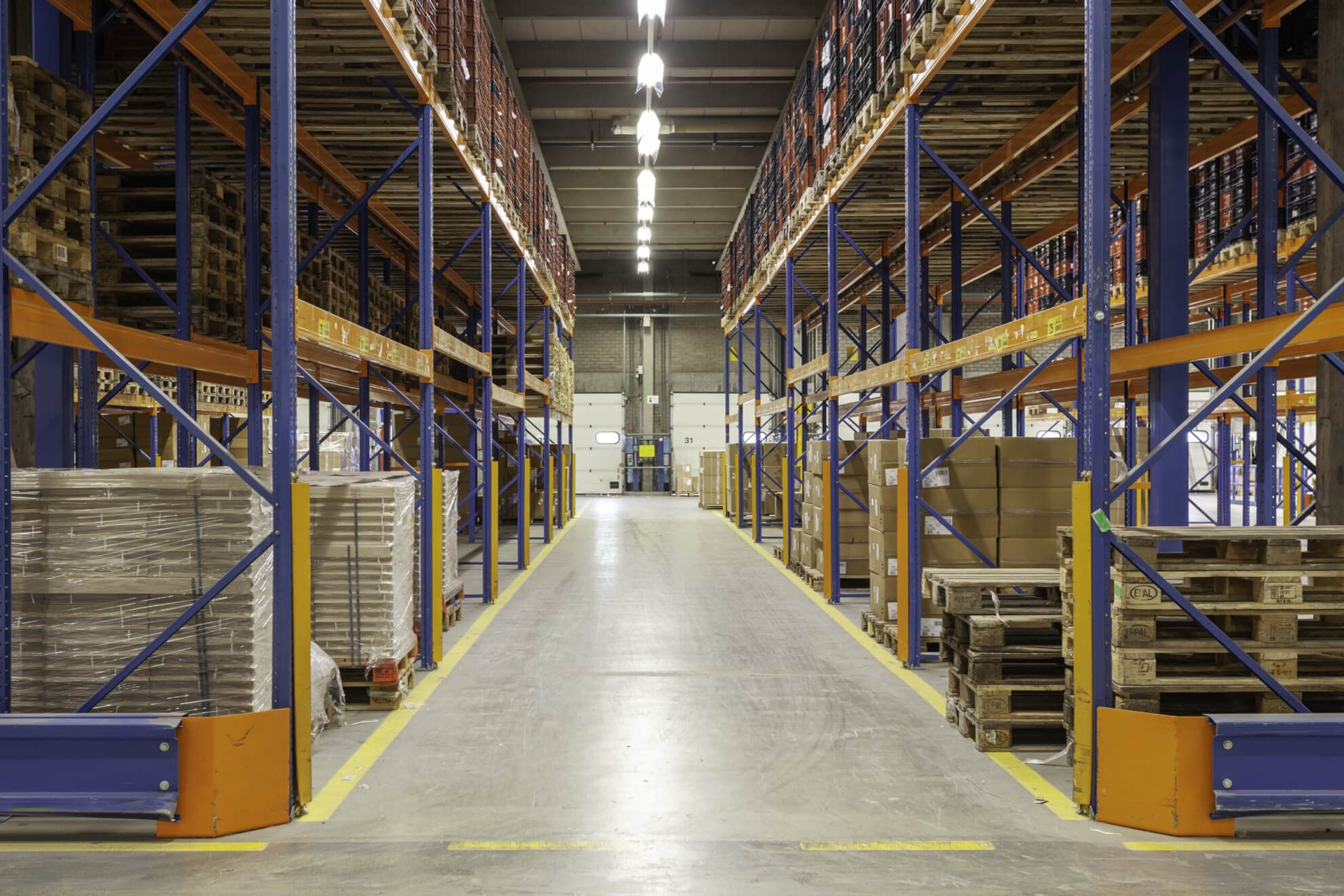
A warehouse mezzanine is a raised platform that is installed between the floor and ceiling of an industrial workplace. Mezzanine floors will be constructed differently based on need, but they are often made with steel, wood or corrugated metal decking. Here are several factors that can affect warehouse mezzanine floor costs.
The Design as a Whole
The most direct factor when it comes to estimating warehouse mezzanine floor costs should be a no-brainer, and that’s its size as a whole. The wider an elevated surface is; the more total materials it will take to finish the particular job. Height needs can also alter the end cost as well.
There are also considerations to be made with column placement, and if it should be increased or decreased based on the kind of activity occurring below the mezzanine’s deck. The taller the platform, along with the much-needed stairway systems needed to reach the mezzanine in question, the larger the entire construction endeavor.
Most of the time, warehouse mezzanine design is kept to a typical rectangle foundation, but other design variations are more than possible. Uncommon shapes typically could potentially lead to uncommon prices when it comes to warehouse mezzanine floor costs.
Mezzanine Floor and Weight Capacity
Expanding an already existing facility, renting out more warehouse space and even buying an entirely new building are all extreme and costly ideas when a warehouse could easily modify a mezzanine to function as an additional storage area or even an office area. If that is the case, then consideration must be made to the PSF (pounds per square foot) that the mezzanine can hold.
It is commonplace that mezzanines carry standard loads of 125 lbs per square foot, but an increase in the weight capacity of the platform will end up requiring larger horizontal beams to be installed, which, ultimately, increases the mezzanine floor cost.
Custom Options
Mezzanine uses differ depending on the client. They can be used for storage space, offices, or even as work platforms. Their purpose sometimes relies on special features for it to function as desired. Handrails would be required on storage-based mezzanines in order to keep items organized within a certain area, along with gate systems for forklifts to place items safely.
Safety Standards
One of the biggest issues when it comes to warehouse mezzanine systems costs is the strict adherence to safety codes and standards, such as the ones set by groups such as OSHA. The larger the platform, the more safety systems, such as handrails and stair width, need be applied to the construction.
Tips for Cost-Effective Mezzanine Floor Construction
Building a mezzanine floor can be a significant investment, but there are several strategies you can employ to ensure that you get the best value for your money while keeping costs in check. Here are some essential tips for cost-effective mezzanine floor construction:
A. Planning and Budgeting
- Clear Project Objectives: Start by defining the purpose of your mezzanine floor. Is it for storage, office space, or additional production capacity? Understanding the intended use will guide your design and budget.
- Detailed Plans: Work closely with an architect or design professional to create detailed plans and specifications. Having a well-thought-out design minimizes costly changes during construction.
- Accurate Measurements: Ensure that all measurements are precise and that the design accounts for existing structures and utilities. This helps prevent costly modifications later on.
- Comprehensive Budget: Create a comprehensive budget that includes all aspects of the project, from materials and labor to permits and inspections. Leave room for contingencies to accommodate unexpected expenses.
B. Choosing the Right Contractor
- Experience Matters: Select a contractor with a proven track record in mezzanine floor construction. Experienced contractors are more likely to deliver quality work within budget and on time.
- References and Reviews: Ask for references and check online reviews from previous clients. This provides insights into the contractor’s reliability and workmanship.
- Competitive Bidding: Obtain multiple quotes from different contractors to compare prices and services. Be cautious of quotes that seem significantly lower than others, as they may result in hidden costs later.
C. Material Selection
- Quality Materials: While it’s tempting to cut costs by using cheaper materials, prioritize quality and durability. High-quality materials may have a higher upfront cost but can lead to long-term savings through reduced maintenance and repairs.
- Consider Pre-Owned Materials: Depending on your project’s requirements, you may explore the option of using pre-owned or recycled materials, which can be more budget friendly.
Warehouse mezzanine floor costs can be complex. Consider taking a look at industrial shelving types offered by Industrial Products Plus for your warehouse needs by contacting us today for a free quote!